Reorganizacja intralogistyki pozwala zwolnić miejsce pod produkcję – case study
Get More Services
ul. Rynek 60/2
50-116 Wrocław
w.podsiadly|getmoreservices.pl| |w.podsiadly|getmoreservices.pl
+48571246669
www.getmoreservices.pl
Zmodyfikowanie przepływu materiałów z uwzględnieniem czasu składowania szybko rotujących ładunków pozwala zaoszczędzić powierzchnię magazynową. W zakładzie AGCO/Fendt udało się w ten sposób zwolnić na potrzeby linii produkcyjnych 1,5 tys. mkw.
Charakterystyka obiektu
Fendt to wiodąca na rynku niemieckim marka maszyn rolniczych należąca do globalnej grupy AGCO. Siedziba przedsiębiorstwa znajduje się w niemieckim Marktoberdorfie. W skali roku spółka produkuje kilkanaście tysięcy ciągników i wypracowuje wpływy przekraczające 8 mld euro. Z linii zakładu firmy każdego dnia zjechać może nawet 100 ciągników oraz około 120 przekładni Vario, dostarczanych następnie do montażu i głównego magazynu części zamiennych. Do 2023 r. roczna przepustowość ma zostać zwiększona o 20 proc. Z myślą o tym procesie rozpoczęto reorganizację logistyki i zaopatrzenia produkcji mającą przygotować zakład do nowych wymagań.
Zastosowane rozwiązanie
Pierwszym krokiem w kierunku osiągnięcia zakładanej w 2023 r. przepustowości była analiza obrotu poszczególnymi komponentami. Przeanalizowano warunki przechowywania, struktury zamówień i proces ich kompletacji. – Sukces projektów takich jak ten w dużej mierze zależy od jakości danych planistycznych. Proces pozyskiwania danych ma więc zasadnicze znaczenie. By móc trafnie zidentyfikować sytuację wyjściową, zgromadziliśmy szczegółowe informacje na temat liczby przetwarzanych i transportowanych komponentów – wyjaśnia odpowiedzialny za wdrożenie w Fendt doradca intralogistyczny STILL, Bernd Geiger. Na podstawie analizy stworzono listę potencjalnych rozwiązań wraz z rekomendacjami uwzględniającymi ocenę poszczególnych wariantów pod kątem takich kryteriów jak: dostępność siły roboczej czy przewidywany czas zwrotu z inwestycji. Wybrana ostatecznie koncepcja pozwala osiągnąć w centrum logistycznym maksymalną efektywność ekonomiczną.
W związku z faktem, że obudowy skrzyń biegów zajmują około 80 proc. pojemności magazynu, stworzono krótkoterminowy magazyn przeładunkowy przewidujący ich składowanie przez zaledwie kilka dni. W toku projektu zidentyfikowano także szybko zbywalne komponenty, z myślą o których stworzono odrębny przepływ materiałów z magazynem tymczasowym. Trafiają do niego części, które nie spędziłyby na półkach więcej niż pół dnia. Docelowo ma on zostać w pełni poddany automatyzacji. Gotowość na przyszłość była istotna także w kontekście magazynu głównego, z regałami wysokiego składowania, wąskimi alejkami i systemowymi wózkami widłowymi. Znajdujące zastosowanie w tej strefie pojazdy VNA serii STIL MX-X wyposażono w system nawigacji STILL iGo pilot, dzięki któremu pojazdy same poruszają się wzdłuż alejki i trafiają do odpowiedniego miejsca paletowego. Do operatora należy jedynie pobieranie i odkładanie ładunków. W razie potrzeby całość procesu można zautomatyzować. – Procesy AGCO/Fendt zaplanowaliśmy z myślą o przyszłości. Zastosowane pojazdy można z łatwością poddać pełen automatyzacji. Pozwala to elastycznie reagować na potrzeby i regulować poziom automatyzacji: od sterowania ręcznego, przez półautomatyczne aż po pełną automatyzację – wyjaśnia Bernd Geiger, konsultant STILL. Obsługa ładunków na niższych kondygnacjach odbywa się z użyciem wózków do kompletacji pionowej STILL OXV 08. Za zasilanie linii produkcyjnych odpowiadają natomiast zestawy transportowe z ciągnikami elektrycznymi.
Efekt wdrożenia
W toku realizacji projektu przekształconych zostało około 80 proc. procesów magazynowych AGCO/Fendt. Zaplanowana reorganizacja systemu składowania w oparciu o wyodrębnienie magazynu tymczasowego i krótkoterminowego pozwoliła usunąć stosowane dotąd wyspy z ładunkami i zwolnić na potrzeby linii montażowych 1,5 tys. mkw. powierzchni. Zastosowane rozwiązania można łatwo zautomatyzować, uzyskując przepustowość przepływu materiałów potrzebną w kontekście planowego zwiększenia produkcji. Realizacja projektu trwała łącznie zaledwie 9 miesięcy, z czego około 75 dni poświęcono na zbieranie, analizę danych oraz stworzenie całościowej koncepcji i harmonogramu prac. Montaż infrastruktury odbył się w ciągu 3 świątecznych tygodni, na modernizacji nie ucierpiał więc plan produkcji.
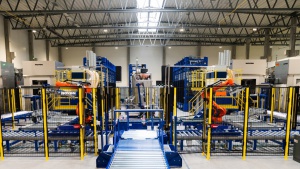
Duże linie myjące: zintegrowane systemy dla wymagającej produkcji

Nowy model myjni przemysłowej NOYEN: Dlaczego warto zainwestować w kompaktowe rozwiązanie mycia detali
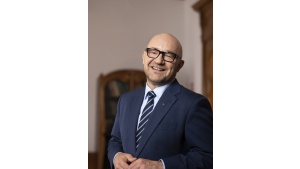
Nowy Prezes Związku Browary Polskie
Więcej ważnych informacji
Jedynka Newserii
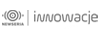
Jedynka Newserii
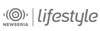
Konsument
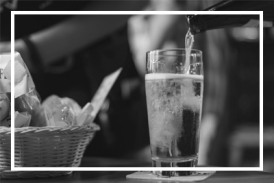
Wzrost sprzedaży piw bezalkoholowych idzie w parze z inwestycjami w zieloną energię. Kompania Piwowarska ogranicza ślad węglowy i wspiera lokalne inicjatywy
Kompania Piwowarska kontynuuję realizację strategii „Lepsza Przyszłość 2030”, w której łączy ambitne cele środowiskowe, edukacja konsumentów oraz rozwój segmentu piw bezalkoholowych z realnym wsparciem dla lokalnych społeczności. Firma, będąca liderem polskiego rynku piwa, ogranicza emisję CO₂, zwiększa udział opakowań zwrotnych i angażuje pracowników w wolontariat, w tym m.in. w pomoc dla ofiar powodzi na Dolnym Śląsku.
Handel
D. Joński: Europa musi chronić swój rynek poprzez cła i wysokie standardy bezpieczeństwa dla importowanych towarów. Powinniśmy budować własny przemysł oparty na tańszej energii
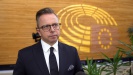
Tańsza energia, a przez to niższe koszty produkcji w Europie to jeden z kierunków, który wskazuje Unia Europejska w rywalizacji z tanimi towarami z Azji, głównie z Chin. Jednocześnie rynek Starego Kontynentu powinien być chroniony poprzez zbalansowane cła oraz wysokie standardy bezpieczeństwa stawiane importowanym produktom. Zdaniem europosła Dariusza Jońskiego ważne jest rozwijanie przemysłu w Europie bez względu na narodowość właścicieli. Relacje z Chinami muszą zostać na nowo zdefiniowane i przebiegać na równych zasadach.
Handel
Poprawia się jakość raportów dużych spółek giełdowych dotyczących zrównoważonego rozwoju. Pozostają też obszary do dopracowania
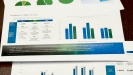
Ekspertki i eksperci z Deloitte’a przeprowadzili analizę ujawnień taksonomicznych spółek notowanych na Giełdzie Papierów Wartościowych, która objęła sprawozdania z działalności za rok 2024 w części dotyczącej zrównoważonego rozwoju. To trzeci rok ujawniania stopnia zgodności przedsiębiorstw z Taksonomią Unii Europejskiej, co przekłada się na zwiększoną jakość i porównywalność prezentowanych danych. Jednocześnie można oczekiwać, że inwestycje zgodne z Taksonomią będą coraz istotniejszym elementem strategii rozwoju przedsiębiorstw w kolejnych latach.
Partner serwisu
Szkolenia
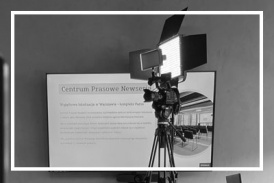
Akademia Newserii
Akademia Newserii to projekt, w ramach którego najlepsi polscy dziennikarze biznesowi, giełdowi oraz lifestylowi, a także szkoleniowcy z wieloletnim doświadczeniem dzielą się swoją wiedzą nt. pracy z mediami.